Dlaczego Gładź Pęka? Poznaj Najczęstsze Przyczyny
Ach, ta gładź! Kto z nas nie marzył o idealnie gładkich ścianach, stanowiących płótno dla wymarzonych kolorów czy faktur? Jednak często ten sen pryska, dosłownie, kiedy pojawiają się na niej szpecące linie. Wielu zadaje sobie pytanie: Dlaczego gładź pęka, niwecząc cały włożony trud i pieniądze? W skrócie, gładź najczęściej pęka z powodu nieprawidłowego przygotowania podłoża lub błędów podczas jej aplikacji i wysychania, a czasem winę ponoszą także ruchy samej konstrukcji budynku.
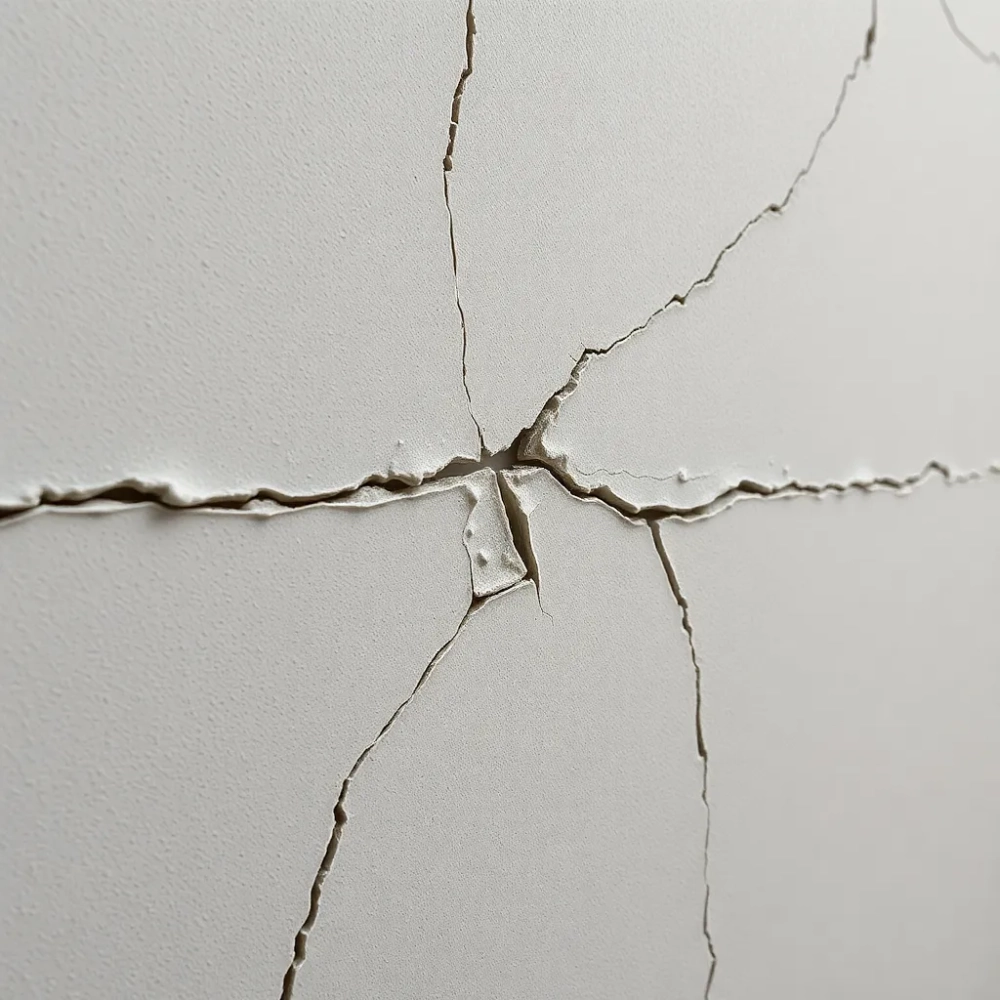
Z przeprowadzonych analiz przypadków z ostatnich lat wynika, że najczęstszymi przyczynami defektów, takich jak pęknięcia gładzi, są czynniki pozostające w bezpośrednim związku z procesem wykonania prac wykończeniowych. Oto przykładowe dane dotyczące potencjalnych źródeł problemów obserwowanych na podstawie setek projektów:
Przyczyna Problemu | Szacunkowa Częstotliwość | Potencjalne Konsekwencje |
---|---|---|
Niewłaściwe przygotowanie podłoża (kurz, słaba spoistość, chłonność) | ~35% przypadków | Adhezja, pęknięcia skurczowe |
Błędy podczas aplikacji (za gruba warstwa, złe proporcje wody, brak siatki) | ~30% przypadków | Pęknięcia strukturalne, kruszenie |
Nieprawidłowe warunki wysychania (temperatura, wilgotność, przeciągi) | ~25% przypadków | Szybkie odparowanie wody, naprężenia skurczowe |
Ruchy konstrukcyjne lub wady podłoża | ~10% przypadków | Pęknięcia przenoszone z podłoża, Rysy na styku materiałów |
Jak widać z powyższego, czynnik ludzki oraz niedostosowanie warunków zewnętrznych odgrywają kluczową rolę w powstawaniu niechcianych rys na finiszowej warstwie tynku. Ignorowanie podstawowych zasad sztuki budowlanej może skutkować kosztownymi naprawami, które pochłaniają czas i zasoby finansowe przewyższające pierwotny koszt prac.
Aby unaocznić potencjalne ryzyko wystąpienia pęknięć w gładzi w zależności od konkretnych przyczyn, przygotowaliśmy poglądowy wykres. Przedstawia on procentowy udział najczęstszych błędów prowadzących do zarysowań na powierzchni ścian, zgodnie z analizami technicznymi. Proszę mieć na uwadze, że są to dane orientacyjne, bazujące na typowych obserwacjach.
Wpływ Przygotowania Podłoża na Trwałość Gładzi
Zanim nałożymy pierwszą warstwę gładzi, musimy zadać sobie podstawowe pytanie: czy podłoże jest w ogóle gotowe na przyjęcie tego delikatnego materiału? Ignorowanie etapu przygotowania podłoża to jak budowanie domu na piasku – katastrofa jest tylko kwestią czasu. Pękanie gładzi często zaczyna się od słabego fundamentu, jakim jest źle przygotowana powierzchnia.
Powierzchnia ściany czy sufitu musi być przede wszystkim czysta i pozbawiona wszelkich luźnych elementów. Stary, kruszący się tynk, resztki farby, kurz, pył budowlany – to wszystko stanowi barierę adhezyjną. Wyobraźcie sobie, że delikatna gładź próbuje przylgnąć do warstwy pyłu; to po prostu fizycznie niemożliwe, aby uzyskała trwałe połączenie.
Częstym problemem jest również niejednorodna chłonność podłoża. Ściany murowane, betonowe stropy, płyty gipsowo-kartonowe – każdy z tych materiałów absorbuje wodę w inny sposób. Nałożenie gładzi bezpośrednio na takie podłoże spowoduje, że w jednych miejscach będzie schnąć błyskawicznie (na bardziej chłonnych fragmentach), a w innych wolniej, co prowadzi do powstawania niekontrolowanych naprężeń wewnętrznych.
Rozwiązaniem problemu nierównomiernej chłonności i słabej adhezji jest zastosowanie odpowiedniego preparatu gruntującego. Gruntowanie wyrównuje chłonność, wzmacnia powierzchnię i poprawia przyczepność. Mamy do wyboru grunty akrylowe, głęboko penetrujące, specjalistyczne pod gładzie czy tynki – wybór zależy od typu podłoża i jego stanu.
Studium przypadku: W pewnym remontowanym mieszkaniu wykonawca postanowił "zaoszczędzić" na gruntowaniu starych, pylących ścian. Gładź została nałożona szybko. Po zaledwie kilku tygodniach pojawiły się mikropęknięcia rozłożone nieregularnie na dużej powierzchni. Wystarczyło przetarcie dłonią, by odpadły drobinki gładzi. Okazało się, że zamiast związania się z podłożem, gładź przywarła jedynie do warstwy kurzu. Koszt naprawy? Dwukrotność pierwotnej ceny usługi i materiałów, ponieważ trzeba było wszystko skuć i zacząć od nowa – tym razem prawidłowo.
Przygotowanie podłoża obejmuje również usunięcie starych warstw, które mogą być źródłem problemów. Farby emulsyjne często wymagają zmatowienia, farby olejne całkowitego usunięcia, a łuszczące się tynki – gruntownego skucia. To etap brudny i czasochłonny, ale absolutnie niezbędny dla trwałości przyszłych warstw.
Minimalna temperatura podłoża i otoczenia podczas gruntowania oraz nakładania gładzi to zwykle +5°C. Niższe temperatury spowalniają, a nawet uniemożliwiają prawidłowe wiązanie spoiw. Zbyt wysoka temperatura (powyżej +25°C) i niskie wilgotności mogą z kolei powodować zbyt szybkie wysychanie gruntów czy gładzi.
Na powierzchniach o dużej chłonności (np. tynki cementowo-wapienne bez gładzi) gruntowanie powinno być wykonane nawet dwukrotnie, z zachowaniem odpowiednich przerw technologicznych (zwykle od 2 do 4 godzin, zależnie od produktu i warunków). Pierwsza warstwa penetruje, druga wyrównuje.
Wilgotność podłoża również ma znaczenie. Nadmiernie mokre podłoże może uniemożliwić wiązanie gładzi lub doprowadzić do jej spękań podczas wysychania, gdy woda uwięziona pod warstwą gładzi będzie parować. Wilgotność murów czy tynków przed gruntowaniem nie powinna przekraczać zazwyczaj 4-6%.
Niejednokrotnie na styku różnych materiałów, np. płyty GK i muru, lub tam, gdzie podłoże ma widoczne pęknięcia, konieczne jest zastosowanie taśmy zbrojącej (np. papierowej, fizelinowej lub siatki z włókna szklanego) wtapianej w pierwszą warstwę gładzi szpachlowej. Brak zbrojenia krytycznych miejsc może skutkować natychmiastowym pojawieniem się rys przeniesionych z podłoża.
Grubość warstwy zbrojącej masy szpachlowej z taśmą na styku płyt GK wynosi zazwyczaj od 0,5 mm do 1 mm po związaniu. Sam skos z płyty GK ma około 45 stopni i głębokość 1-2 mm. Poprawne wypełnienie i zbrojenie tych połączeń jest fundamentalne dla zapobiegania pęknięciom w przyszłości.
Powierzchnia po przygotowaniu (usunięciu luźnych części, zagruntowaniu) powinna być jednolita, stabilna i sucha. Delikatne przetarcie dłonią nie powinno powodować osypywania się pyłu. To prosta, choć często ignorowana próba.
Koszty związane z przygotowaniem podłoża to często tylko niewielki procent całościowych kosztów prac tynkarskich i malarskich, zazwyczaj w granicach 5-10%. Za litr dobrego gruntu zapłacimy od kilkunastu do kilkudziesięciu złotych, a jego wydajność to często 5-10 m²/l. Ignorując ten koszt, ryzykujemy znacznie większe wydatki na poprawki, które mogą wynieść nawet 50-100% pierwotnego kosztu położenia gładzi.
Doświadczeni wykonawcy zawsze podkreślają, że "pośpiech jest złym doradcą" na etapie przygotowania podłoża. Każda wada na tym etapie zostanie bezlitośnie ujawniona przez cienką warstwę gładzi. Nawet najlepsza gładź i najdroższa farba nie zamaskują błędów popełnionych na początku.
Zdarza się, że podłożem jest stary tynk cementowo-wapienny, który jest nierówny i ma wiele drobnych rys skurczowych. W takim przypadku, oprócz gruntowania, rozważyć należy zatopienie siatki zbrojącej na całej powierzchni ściany w pierwszej warstwie gładzi szpachlowej. Gramatura siatki to często 145-160 g/m², a grubość pierwszej warstwy gładzi powinna wynosić 1-2 mm.
Kontrola podłoża przed rozpoczęciem prac jest kluczowa. Należy sprawdzić spoistość (np. poprzez zarysowanie), chłonność (test wodny – kapanie wody i obserwowanie, jak szybko wsiąka) oraz czystość. Nie bez znaczenia jest też pH podłoża, które dla większości gładzi powinno być obojętne lub lekko zasadowe (pH 7-9).
Zbagatelizowanie tych podstawowych czynności prowadzi do frustracji, kiedy pomalowane ściany zamiast zachwycać gładkością, prezentują sieć pajączków. To smutna lekcja o tym, że trwałość gładzi zależy bezpośrednio od solidności przygotowania podłoża.
Przygotowanie podłoża to proces, który może zająć nawet jeden lub dwa dni dla typowego pokoju o powierzchni 20-30 m², wliczając w to czas schnięcia gruntu. W obliczu późniejszych potencjalnych problemów i kosztów, jest to inwestycja, która po prostu się opłaca.
Błędy Aplikacyjne Skutkujące Pęknięciami Gładzi
Nawet perfekcyjnie przygotowane podłoże nie zagwarantuje sukcesu, jeśli gładź zostanie nałożona niewłaściwie. Błędy aplikacyjne to chyba najszersza kategoria przyczyn pękania gładzi, często wynikająca z pośpiechu, braku doświadczenia lub niestosowania się do zaleceń producenta materiału. Wiecie co? Niechlujna aplikacja gładzi to pewna droga do pęknięć i zmarnowanych materiałów.
Jednym z najczęstszych grzechów jest przygotowanie gładzi o złej konsystencji. Za dużo wody sprawia, że masa jest rzadka, trudna w nakładaniu, ma mniejszą wytrzymałość i jest bardziej podatna na skurcz. Za mało wody – masa jest gęsta, trudno się rozprowadza, tworzy zgrubienia i nierówności.
Producent zawsze podaje na opakowaniu dokładne proporcje mieszania suchej mieszanki z wodą, np. 0,4 litra wody na 1 kg proszku, lub zalecane ilości na całe opakowanie (np. 10 litrów wody na 25 kg gładzi). Odchylenie od tych proporcji o więcej niż 5-10% jest ryzykowne. Z doświadczenia wiemy, że lekko gęstsza konsystencja jest często wybierana przez mniej doświadczonych aplikatorów, by łatwiej uzyskać równą powierzchnię, ale może to prowadzić do pęknięć, zwłaszcza przy grubszych warstwach.
Innym kardynalnym błędem jest nakładanie zbyt grubych pojedynczych warstw. Standardowa grubość jednej warstwy gładzi finiszowej to zazwyczaj 1-2 mm. Gładzie szpachlowe, stosowane do wyrównania większych ubytków, mogą być kładzione grubiej (do 3-5 mm jednorazowo, a nawet więcej w przypadku specjalistycznych produktów), ale zawsze zgodnie z zaleceniami producenta. Aplikacja gładzi w zbyt grubych warstwach powoduje powstawanie wewnętrznych naprężeń podczas schnięcia, prowadząc do rys.
Podczas nakładania kolejnych warstw gładzi, poprzednia musi być wystarczająco sucha i związana. Nakładanie "mokre na mokre" lub na warstwę, która jeszcze intensywnie schnie, uniemożliwia prawidłowe odparowanie wody z dolnych partii, co prowadzi do wewnętrznych naprężeń i delaminacji warstw. Czas schnięcia jednej warstwy (1-2 mm) w optymalnych warunkach (temperatura 20°C, wilgotność 60%) wynosi zazwyczaj 12-24 godzin. W chłodniejszych lub bardziej wilgotnych warunkach może być znacznie dłuższy, nawet 48 godzin.
Mieszanie gładzi – to też ma znaczenie. Niewłaściwe mieszanie (za krótko, za szybko, zbyt wolno, bez odstawienia do dojrzenia) może pozostawić niezwiązane cząsteczki spoiwa lub wprowadzić zbyt wiele powietrza. Masa powinna być jednolita i gładka po mieszaniu, bez grudek i bąbli powietrza.
Bardzo ważne jest także prawidłowe szpachlowanie narożników wewnętrznych i zewnętrznych. Narożniki wewnętrzne często wymagają zbrojenia taśmą (papierową, fizelinową) lub zastosowania specjalistycznych mas elastycznych. W narożnikach zewnętrznych stosuje się metalowe lub plastikowe narożniki ochronne. Nieprawidłowe wykończenie narożników to częsta przyczyna pęknięć w tych krytycznych miejscach.
Narożnik wewnętrzny bez zbrojenia, szczególnie na styku dwóch płaszczyzn, które mogą pracować niezależnie (np. ściana działowa i ściana nośna, ściana i sufit), jest niemal gwarantem pęknięcia. Koszt rolki taśmy papierowej to kilkanaście złotych, a daje niemal 100% pewność trwałości połączenia, w porównaniu do pewności 0% bez taśmy.
Nie bez znaczenia jest narzędzie, którym aplikowana jest gładź. Czyste i równe pace stalowe, kielnie, szpachle – to podstawa. Brudne narzędzia mogą wnosić zanieczyszczenia, a nierówne lub zużyte zostawiać bruzdy i nierówności wymagające grubszej warstwy maskującej.
Aplikator powinien prowadzić narzędzie pewnie i równomiernie, starając się uzyskać jak najcieńszą i najbardziej równą warstwę w pierwszej kolejności. Następnie ewentualnie korygować i dokładać materiał, ale zawsze dbając o to, aby grubość warstwy była kontrolowana.
Szlifowanie – choć to etap post-aplikacyjny, sposób jego wykonania może również wpłynąć na pękanie. Zbyt wczesne szlifowanie mokrej lub niedostatecznie związanej gładzi uszkadza jej strukturę wewnętrzną. Zbyt intensywne szlifowanie zbyt suchą gładzią może nagrzać powierzchnię, co teoretycznie może wpływać na naprężenia, choć jest to rzadsza przyczyna pęknięć.
Pamiętajcie o tzw. "czasie życia" gotowej masy szpachlowej (jeśli jest gotowa do użycia w wiaderku) lub o czasie od jej wymieszania z wodą (dla gładzi w proszku). Przeterminowana lub zbyt długo przetrzymywana masa traci swoje właściwości i jest bardziej podatna na defekty, w tym pękanie.
Nieraz wykonawcy w celu przyspieszenia prac stosują zbyt intensywne suszenie (np. dmuchawy ciepłego powietrza). Jak ognia należy unikać takich praktyk. Zbyt szybkie odparowanie wody z powierzchniowej warstwy prowadzi do natychmiastowego powstawania silnych naprężeń skurczowych i gładź będzie pękać niczym wyschnięta ziemia na pustyni.
Podsumowując, błędna aplikacja to złożony problem, często wynikający z niedostatecznej staranności, pośpiechu i braku podstawowej wiedzy o zachowaniu materiału. Nawet drobne odchylenia od prawidłowej technologii mogą doprowadzić do powstania rys na powierzchni, które później trudno usunąć bez gruntownych poprawek.
Koszt materiału do wykonania gładzi na typowy pokój 20 m² to kilkadziesiąt do kilkuset złotych, zależnie od rodzaju gładzi (polimerowa, gipsowa, gotowa). Koszt robocizny to od kilkunastu do kilkudziesięciu złotych za m². Dodatkowe koszty związane z poprawkami spowodowanymi błędami aplikacji mogą łatwo podwoić lub potroić pierwotny budżet. Lepiej zrobić raz a dobrze.
Rola Temperatury i Wilgotności Powietrza podczas Wysychania Gładzi
Warunki atmosferyczne w pomieszczeniu, w którym schnie gładź, mają absolutnie kluczowe znaczenie dla jej finalnej wytrzymałości i gładkości. Ignorowanie temperatury i wilgotności podczas procesu wysychania to proszenie się o kłopoty. Warunki otoczenia decydują o tym, czy gładź zwiąże się poprawnie, czy popęka.
Gładzie gipsowe i polimerowe, a także gotowe masy, potrzebują optymalnych warunków do prawidłowego wyschnięcia i uzyskania pełnej wytrzymałości. Generalnie, idealne warunki to temperatura powietrza w zakresie od +10°C do +25°C i wilgotność względna powietrza pomiędzy 40% a 65%.
Co się dzieje, gdy temperatura jest za niska, powiedzmy poniżej +5°C? Proces hydratacji (wiązania gipsu z wodą) lub polimeryzacji jest spowolniony lub całkowicie zatrzymany. Gładź nie wiąże prawidłowo, pozostaje "miękka", podatna na uszkodzenia i z pewnością nie osiągnie deklarowanych przez producenta parametrów wytrzymałościowych. Ryzyko pęknięć związanych z niedowiązaniem jest bardzo wysokie.
Z drugiej strony, co gdy temperatura jest za wysoka, na przykład powyżej +30°C, lub co gorsza, towarzyszy jej niska wilgotność powietrza (poniżej 30%)? W takich warunkach woda z gładzi odparowuje zbyt szybko, zwłaszcza z warstwy powierzchniowej. Powierzchnia twardnieje, podczas gdy niższe warstwy są jeszcze wilgotne i kurczą się wolniej. Powstają olbrzymie naprężenia skurczowe między wysychającą powierzchnią a wolniej schnącymi wewnętrznymi warstwami. Efekt? Typowe, drobne siateczkowe pęknięcia, czasem głębsze rysy. To jak z wyschniętym błotem.
Przeciągi to kolejny wróg gładkiej powierzchni. Otwarte okna i drzwi powodują intensywny, niekontrolowany ruch powietrza, który gwałtownie przyspiesza wysychanie powierzchni gładzi. Działa to podobnie jak wysoka temperatura i niska wilgotność – powierzchnia wysycha za szybko w stosunku do wnętrza masy, co prowadzi do pęknięć. Lepiej zapewnić łagodne wietrzenie po wstępnym związaniu masy, np. po kilku godzinach, otwierając okna tylko uchylnie na krótko, lub używać wentylacji mechanicznej z odzyskiem ciepła, która cyrkuluje powietrze, ale bez tworzenia intensywnych strumieni.
W przypadku zbyt niskiej wilgotności można zastosować nawilżacze powietrza lub rozwiesić wilgotne tkaniny w pomieszczeniu. Ważne jednak, by nie doprowadzić do skraplania wody na powierzchni gładzi, co również byłoby szkodliwe.
Czas schnięcia gładzi jest ściśle zależny od grubości warstwy, rodzaju materiału (gipsowa, polimerowa, cementowa), temperatury i wilgotności. Typowa warstwa gładzi finiszowej (1-2 mm) w optymalnych warunkach schnie około 24 godzin. W warunkach gorszych, ten czas może wydłużyć się do 48-72 godzin. Malowanie lub szlifowanie przed pełnym wyschnięciem to błąd.
Zdarza się, że inwestor lub wykonawca próbuje przyspieszyć wysychanie prac, kierując na gładź grzejniki elektryczne, farelki lub nagrzewnice. To barbarzyństwo dla materiału! Zbyt szybkie, wymuszone schnięcie jest jedną z głównych przyczyn pęknięć gładzi.
Kontrola warunków jest stosunkowo prosta – wystarczy termometr i higrometr. Koszt takiego zestawu to kilkadziesiąt złotych. Wydaje się to drobiazg, ale to kluczowe narzędzie do zapewnienia trwałości gładzi.
Wilgotność podłoża również wpływa na proces wysychania gładzi. Jeśli podłoże jest nadmiernie wilgotne, spowalnia to wysychanie dolnych warstw gładzi, podczas gdy warstwa zewnętrzna schnie szybciej pod wpływem powietrza. Powoduje to nierównomierne naprężenia skurczowe. Maksymalna dopuszczalna wilgotność podłoża przed nałożeniem gładzi to zwykle 4-6%.
W przypadku nowo budowanych domów, gdzie ściany i stropy mają dużą wilgotność technologiczną, bardzo ważne jest, aby pozwolić konstrukcji na wstępne wyschnięcie (tzw. "odparowanie wody zarobowej") przez kilka tygodni, a nawet miesięcy, zanim zaczniemy prace tynkarskie i szpachlowe. Zamykanie wilgoci pod szczelną warstwą gładzi to proszenie się o późniejsze problemy.
Reasumując, stworzenie stabilnych i optymalnych warunków temperaturowo-wilgotnościowych podczas schnięcia gładzi jest równie ważne, jak jakość samego materiału i staranność aplikacji. To czas, w którym materiał "pracuje" i osiąga swoje parametry. Warto poświęcić mu uwagę.
Koszt zapewnienia odpowiednich warunków może oznaczać potrzebę zakupu lub wynajęcia osuszaczy powietrza (np. dla nowo wybudowanych obiektów), ogrzewania lub wentylacji. Dzienny koszt wynajmu osuszacza profesjonalnego może wynosić od kilkudziesięciu do ponad stu złotych. Z pewnością jest to wydatek mniejszy niż koszt kucia i ponownego nakładania pękającej gładzi.
Dbając o warunki wysychania, zapewniamy gładzi idealne "środowisko" do związania. Pamiętajcie: gładź to nie farba, która wysycha głównie przez odparowanie rozpuszczalnika; to materiał budowlany, który musi przejść przez proces hydratacji lub polimeryzacji, co wymaga czasu i odpowiedniej ilości wody oraz odpowiedniej temperatury.
Ruchy Konstrukcyjne Budynku a Pękanie Gładzi
Budynki, zwłaszcza nowe, nieustannie "żyją". Osadzają się, pracują pod wpływem zmian temperatury, wiatru czy obciążeń użytkowych. Te ruchy, choć często niewidoczne gołym okiem, potrafią wywołać naprężenia, które najdelikatniejsza warstwa na powierzchni – gładź – bezlitośnie ujawni w postaci rys. Gładź jest niczym sejsmograf ujawniający ruchy konstrukcyjne budynku.
Najczęstszą przyczyną pęknięć związanych z ruchem konstrukcji jest osiadanie budynku. Nowo wybudowane obiekty osiadają przez pierwsze miesiące, a nawet lata. Proces ten jest naturalny, ale powoduje delikatne zmiany geometrii elementów konstrukcyjnych (ścian, stropów, fundamentów). Gładź nałożona zbyt wcześnie, zanim ustabilizuje się konstrukcja, jest szczególnie narażona na pęknięcia osiadające, często biegnące pionowo lub ukośnie.
Problemem są również pęknięcia termiczne. Materiały budowlane (beton, cegła, tynki) rozszerzają się i kurczą pod wpływem zmian temperatury. Dotyczy to zwłaszcza dużych, nieprzerwanych powierzchni. Pęknięcia termiczne często pojawiają się w miejscach o największych naprężeniach, np. przy oknach i drzwiach, gdzie występują zmiany przekroju ściany.
Wibracje, choć rzadziej niż osiadanie czy zmiany termiczne, mogą również przyczyniać się do powstawania pęknięć, zwłaszcza w budynkach zlokalizowanych w pobliżu ruchliwych dróg, linii kolejowych czy terenów, gdzie prowadzone są prace budowlane wykorzystujące ciężki sprzęt (np. wbijanie pali). Pęknięcia od wibracji są zazwyczaj drobne i tworzą "siateczkę".
Szczególnie narażone na pękanie są styki materiałów o różnej charakterystyce i współczynniku rozszerzalności, np. muru i elementów żelbetowych (nadproża, wieńce), muru i lekkich ścian działowych z płyt GK, lub nawet na styku starego i nowego tynku. Różnice w pracy tych materiałów powodują naprężenia w strefie styku.
W takich miejscach, a także w miejscach gdzie spodziewane są większe naprężenia (narożniki okienne, drzwiowe, dylatacje konstrukcyjne), konieczne jest stosowanie odpowiednich systemów zbrojących. Najpopularniejszym rozwiązaniem jest zatopienie taśmy zbrojącej (z włókna szklanego lub papierowej) w warstwie gładzi szpachlowej. Na dylatacjach stosuje się specjalne profile lub sznury dylatacyjne z masami elastycznymi.
Pęknięcia na styku ścian murowanych i sufitów z płyt GK są nagminne, jeśli nie zostaną odpowiednio zabezpieczone. Ściana pracuje niezależnie od sufitu. W takim przypadku stosuje się profil ślizgowy (np. F-profil aluminiowy lub plastikowy), który pozwala na niezależne ruchy konstrukcji. Gładź szpachlowa nie jest wtedy nakładana na sztywno na styk obu płaszczyzn, ale na profil lub pozostawiony odstęp wypełniony masą elastyczną.
Czas potrzebny na wstępne osiadanie konstrukcji to często minimum kilka miesięcy od zakończenia głównych prac konstrukcyjnych. W przypadku dużych obiektów ten okres może być dłuższy. Wykonywanie prac wykończeniowych zbyt wcześnie, w intensywnej fazie osiadania, jest ryzykowne.
Małe pęknięcia włoskowate (mikrorysy do 0,2 mm szerokości) mogą pojawić się nawet przy poprawnym wykonaniu prac i być wynikiem normalnych, niewielkich ruchów. Często są maskowane przez elastyczne farby nawierzchniowe. Większe rysy, wymagające interwencji, zazwyczaj świadczą o poważniejszym problemie z podłożem, ruchem konstrukcyjnym lub błędami w zbrojeniu krytycznych miejsc.
Warto wiedzieć, że rodzaj materiału, z którego wykonana jest konstrukcja, wpływa na potencjalne ruchy i ryzyko pękania. Konstrukcje prefabrykowane mogą pracować inaczej niż tradycyjnie murowane. Płyty gipsowo-kartonowe same w sobie są bardziej podatne na pęknięcia na łączeniach, jeśli nie zostaną poprawnie spoinowane i zbrojone.
Studium przypadku: W nowym domu szkieletowym (lekka konstrukcja, która pracuje bardziej niż murowana) pominięto prawidłowe zbrojenie wszystkich narożników wewnętrznych i zewnętrznych płyt OSB oraz GK. Po pół roku na niemal wszystkich łączeniach w rogach ścian pojawiły się rysy, a w okolicach okien nawet drobne pęknięcia ukośne. Problem leżał w niedocenieniu naturalnych ruchów drewna i konstrukcji lekkiej. Konieczne było usunięcie gładzi w strefach pęknięć, zbrojenie łączeń taśmą, a następnie ponowne szpachlowanie i malowanie – duży i kosztowny kłopot.
Przed przystąpieniem do gładzenia w nowym budynku, warto porozmawiać z kierownikiem budowy o etapie osiadania konstrukcji i ewentualnych specyficznych wymaganiach co do wykończenia (np. zastosowanie elastycznych mas, profili dylatacyjnych). Ignorowanie tych aspektów może słono kosztować.
Dylatacje konstrukcyjne (szczeliny celowo pozostawione w konstrukcji, aby umożliwić jej ruch) muszą być bezwzględnie przeniesione na powierzchnię ściany i sufitu. Zaszpachlowanie dylatacji konstrukcyjnej jest przepisem na natychmiastowe pęknięcie w tym miejscu, zazwyczaj szerokie i nieestetyczne.
W starych budynkach pęknięcia związane z ruchem konstrukcyjnym są zazwyczaj stabilniejsze, chyba że dochodzi do zmian w samej konstrukcji (np. usunięcie ściany nośnej, dobudowa). W starszych obiektach problemem mogą być raczej lokalne uszkodzenia podłoża, stare zbrojenia lub nierówne łączenia, które wymagają dokładnego przygotowania przed gładzeniem.
Podsumowując, gładź nie jest materiałem, który magicznie maskuje wady konstrukcyjne. Jest warstwą finalną, która reaguje na to, co dzieje się pod spodem. Zrozumienie potencjalnych ruchów budynku i odpowiednie przygotowanie (lub opóźnienie) prac jest kluczowe dla uniknięcia frustracji i kosztów poprawek. Zbrojenie newralgicznych miejsc nie jest luksusem, a koniecznością wynikającą z fizyki materiałów.