Gładź do spoinowania płyt GK 2025
Witaj w fascynującym świecie wykończenia wnętrz! Jeśli marzysz o idealnie gładkich ścianach i sufitach, to z pewnością zastanawiasz się, czym właściwie jest i do czego służy gładź do spoinowania płyt GK. Krótko mówiąc, jest to kluczowy element do stworzenia jednolitej powierzchni, który pozwala na skuteczne łączenie płyt gipsowo-kartonowych, maskując przy tym wszelkie nierówności i szczeliny.
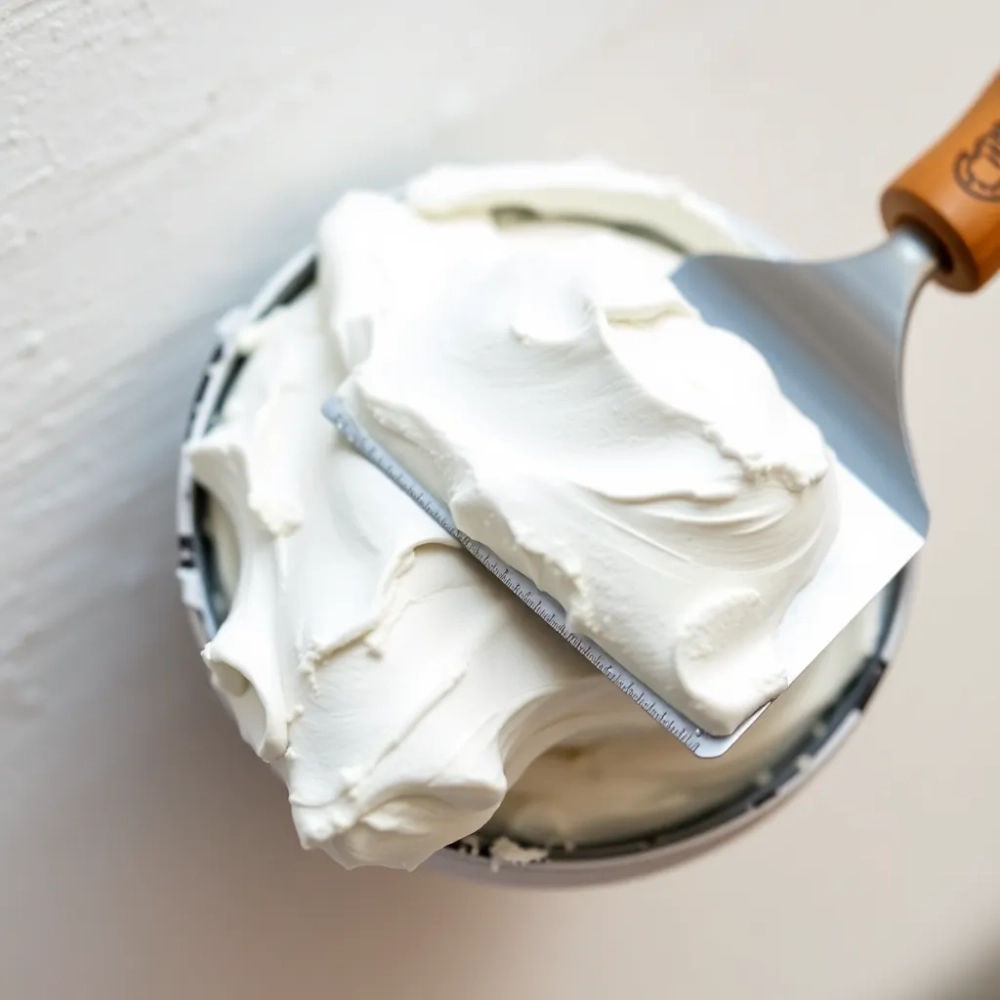
Spoinowanie płyt gipsowo-kartonowych to proces, który na pierwszy rzut oka może wydawać się prosty, ale jak to często bywa w budownictwie, diabeł tkwi w szczegółach. Wybór odpowiedniego materiału, jak właśnie gładź do spoinowania płyt GK, oraz precyzyjne wykonanie każdego kroku, od przygotowania podłoża po ostateczne szlifowanie, ma kolosalne znaczenie dla końcowego efektu. Można to porównać do pieczenia chleba – niby proste, ale tylko precyzja i jakość składników zapewnią idealny bochenek.
Przyjrzyjmy się teraz bliżej niektórym aspektom, które wpływają na proces spoinowania. Zrozumienie ich pomoże uniknąć frustracji i uzyskać wymarzony rezultat. Poniższa tabela przedstawia przykładowe zależności, które mogą wpływać na sukces prac spoinowania:
Czynniki wpływające | Skutki | Przykładowe wartości | Wpływ na wynik końcowy |
---|---|---|---|
Temperatura powietrza | Czas schnięcia | 10°C - 25°C | Zbyt niska lub wysoka temperatura może spowolnić lub przyspieszyć schnięcie, prowadząc do pęknięć. |
Wilgotność podłoża | Przyczepność gładzi | Poniżej 5% | Zbyt wilgotne podłoże może osłabić przyczepność gładzi. |
Wielkość szczelin | Liczba warstw gładzi | Do 3 mm | Większe szczeliny wymagają większej liczby warstw, co wydłuża czas pracy. |
Rodzaj taśmy zbrojącej (jeśli używana) | Wytrzymałość połączenia | Taśma papierowa, fizelinowa, z siatki | Nieodpowiednia taśma może prowadzić do pękania spoiny. |
Jakość gładzi | Łatwość aplikacji i trwałość | Gładź gotowa do użycia z włóknami | Wysokiej jakości produkt ułatwia pracę i zapewnia trwałe połączenia. |
Jak widać, nawet tak prozaiczna rzecz jak temperatura otoczenia może mieć wpływ na ostateczny rezultat. Niewłaściwe przygotowanie podłoża to proszenie się o kłopoty. Wyobraźmy sobie artystę malującego na brudnym płótnie – nawet najlepsza farba nie pokryje zanieczyszczeń i nie stworzy idealnego obrazu. Podobnie jest ze spoinowaniem. Czyste, suche i odpowiednio przygotowane powierzchnie to absolutna podstawa. A potem, krok po kroku, precyzyjnie aplikujemy gładź, dając jej czas na spokojne wyschnięcie. To nie wyścig z czasem, a raczej maraton, gdzie każdy etap ma swoje znaczenie i wymaga cierpliwości.
Rodzaje gładzi do spoinowania płyt GK
Zanurzmy się w świat gładzi, tego magicznego składnika, który potrafi zmienić surowe połączenia płyt gipsowo-kartonowych w niewidoczne szwy idealnie gładkiej ściany. Na rynku dostępnych jest kilka rodzajów tego specyfiku, a wybór odpowiedniego to klucz do sukcesu. Zacznijmy od najnowszych osiągnięć techniki, czyli od gładzi polimerowych zawierających specjalne włókna.
Takie produkty, jak wspomniana alabaster® FINISH CONNECT, to prawdziwy game changer. Charakteryzują się tym, że pozwalają na spoinowanie bez konieczności stosowania taśmy zbrojącej. Dzieje się tak dzięki zawartym w nich włóknom fibrylizowanym, które tworzą swego rodzaju zbrojenie wewnętrzne spoiny. Wyobraź sobie maleńkie, niewidoczne niteczki, które splatają się wewnątrz gładzi, nadając jej niesamowitą wytrzymałość i elastyczność.
Takie gładzie polimerowe z włóknami są zazwyczaj gotowe do użycia, co jest ogromną zaletą. Otwierasz opakowanie, mieszasz i aplikujesz. Proste jak drut! Nie ma potrzeby mieszania z wodą, co eliminuje ryzyko popełnienia błędu w proporcjach i pozwala na uzyskanie idealnej konsystencji od razu. To tak, jakbyś miał gotową pastę do zębów, zamiast musieć ją samemu mieszać z proszku.
Wszechstronność to kolejna cecha, która wyróżnia te nowoczesne gładzie. Oprócz tradycyjnego spoinowania płyt gipsowo-kartonowych z krawędziami zespolonymi (półokrągłymi, spłaszczonymi) czy ostrymi (ściętymi), mogą być również stosowane do łączenia płyt gipsowo-włóknowych czy płyt suchego jastrychu. Pomyśl o nich jako o szwajcarskim scyzoryku w świecie gładzi – przydają się do wielu zadań.
Co więcej, te same gładzie często doskonale sprawdzają się do uzupełniania pęknięć, rys i drobnych ubytków na powierzchni ścian i sufitów. Zamiast kupować kilka różnych produktów, wystarczy jeden uniwersalny, który poradzi sobie z wieloma niedoskonałościami. To oszczędność miejsca w narzędziowni i portfela.
Aplikacja takiej gładzi to czysta przyjemność. Jest gładka, plastyczna i doskonale przylega do podłoża. Przypomina trochę masło rozsmarowywane na ciepłym chlebie – gładkie, bez oporów, po prostu przyjemne. Gładź gotowa bardzo łatwo się aplikuje pacą metalową i pięknie poddaje obróbce, zarówno na etapie nakładania, jak i późniejszego szlifowania.
Kluczem do sukcesu jest doskonała przyczepność do różnych podłoży budowlanych. Tego typu gładź doskonale wiąże się z podłożami gipsowymi, ale też z gazobetonem, tynkami cementowymi, cementowo-wapiennymi czy podłożami betonowymi. Ta wszechstronność sprawia, że jest to idealny wybór nie tylko do nowych budów, ale także podczas remontów, gdzie mamy do czynienia z różnymi rodzajami materiałów budowlanych.
Tradycyjne gładzie do spoinowania często wymagały zastosowania taśmy papierowej lub fizelinowej w celu zbrojenia spoiny. Taśma ta miała za zadanie przenieść naprężenia wynikające z pracy konstrukcji i zapobiec pękaniu gładzi w miejscach łączeń. Stosowanie taśmy wymagało większej precyzji i dodatkowego czasu na jej wklejenie i zatopienie w gładzi. Można to porównać do zbrojenia betonu – taśma działała jak pręty zbrojeniowe w betonie.
Gotowe gładzie do spoinowania bez taśmy upraszczają proces i przyspieszają prace. To duża wygoda, szczególnie dla osób, które spoinują rzadziej lub cenią sobie szybkość wykonania. Niemniej jednak, gładzie do spoinowania wymagające taśmy nadal są w użyciu i w niektórych przypadkach mogą być preferowane ze względu na specyficzne właściwości, takie jak większa twardość po wyschnięciu czy nieco niższa cena.
Warto wspomnieć o czasie wiązania. Gładzie różnią się pod tym względem. Niektóre wiążą chemicznie, inne schną w procesie odparowania wody. Te wiążące chemicznie zazwyczaj szybciej uzyskują pełną wytrzymałość, co przyspiesza postęp prac. Z kolei te schnące wolniej mogą dawać więcej czasu na korygowanie i wygładzanie. Wybór zależy od indywidualnych preferencji i tempa pracy.
Na koniec, przechowywanie i termin ważności. Gładź gotowa do użycia, jak alabaster® FINISH CONNECT, powinna być przechowywana w oryginalnym, szczelnie zamkniętym opakowaniu, w temperaturze od 0°C do 30°C, chroniona przed bezpośrednim nasłonecznieniem, przegrzaniem i przemrożeniem. Pamiętaj, że przydatność produktu po otwarciu opakowania jest ograniczona. Warto zwrócić uwagę na informacje podane przez producenta na opakowaniu. Otwarte opakowanie najlepiej zużyć w ciągu kilku dni lub tygodni, w zależności od zaleceń i warunków przechowywania. To trochę jak z produktami spożywczymi – otwarte opakowanie jogurtu nie przetrwa w lodówce wiecznie.
Jak prawidłowo spoinować płyty GK - krok po kroku
Zatem zabieramy się do roboty! Prawidłowe spoinowanie płyt GK to nie sztuka czarna magia, ale wymaga metodycznego podejścia i trzymania się pewnych zasad. Pamiętaj, że od tego zależy wygląd finalnej powierzchni, na której położysz farbę czy tapetę. To trochę jak budowanie domu – fundamenty muszą być solidne, żeby cała konstrukcja była stabilna. Tutaj fundamentem jest idealna spoina.
Krok pierwszy i absolutnie fundamentalny to przygotowanie podłoża. Płyty GK, które będziesz spoinować, muszą być stabilnie zamocowane do konstrukcji nośnej. Żadne chybotliwe, latające płyty nie wchodzą w grę. Muszą być suche, bez śladów wilgoci, która mogłaby negatywnie wpłynąć na wiązanie gładzi. Co równie ważne, muszą być absolutnie czyste. Żadnego kurzu, żadnych drobinek gipsu, żadnych resztek materiałów budowlanych. Jak chirurg przygotowujący stół operacyjny – wszystko musi być jałowe i gotowe do zabiegu.
Jeśli masz do czynienia z płytami o krawędziach ciętych (ostrych), musisz je koniecznie sfazować. Co to znaczy sfazować? To po prostu ściąć krawędź pod kątem około 45 stopni na głębokość około 2-3 mm. Ten skos tworzy przestrzeń dla gładzi, pozwalając na pełne wypełnienie spoiny. Gdy krawędzie są już sfazowane (lub jeśli masz płyty o krawędziach fabrycznych, które nie wymagają fazowania), należy je dokładnie odpylić. Możesz użyć pędzla lub odkurzacza. Następnie, kluczowy etap – zagruntować. Zastosowanie odpowiedniego gruntu, np. z rodziny alabaster®, zapewni lepszą przyczepność gładzi do podłoża i zredukuje jej wchłanianie, co zapobiega szybkiemu odciągnięciu wody z gładzi i ewentualnym pęknięciom. Gruntowanie to taki bufor bezpieczeństwa, który zapewnia, że gładź zrobi to, co do niej należy, a nie zostanie "wypita" przez płytę.
Jeśli płyty są mocowane wkrętami, pamiętaj, aby łby wkrętów były lekko wpuszczone poniżej powierzchni płyty. Te miejsca również wymagają szpachlowania. Po związaniu gruntu (lub bez gruntu, jeśli płyty fabryczne są gotowe do spoinowania bez tego etapu), możesz przystąpić do pracy z gładzią. W przypadku płyt o krawędziach fabrycznych typu HRAK, HKS czy VARIO, które mają specjalne, spłaszczone lub półokrągłe krawędzie, nie ma potrzeby ich fazowania.
Krok drugi – przygotowanie gładzi. Jeśli używasz gładzi gotowej do użycia, jak alabaster® FINISH CONNECT, sprawa jest prosta. Otwierasz opakowanie i dokładnie mieszasz zawartość pojemnika za pomocą mieszadła koszykowego na wolnych obrotach. Mieszaj, aż uzyskasz jednolitą, gładką konsystencję, bez grudek. I co ważne: nie rozcieńczaj produktu wodą! To częsty błąd początkujących, który może zaburzyć właściwości gładzi i prowadzić do problemów ze schnięciem czy pękaniem. To jak dodawanie wody do farby, która już ma idealną konsystencję – efekt nie będzie ten sam.
Krok trzeci – aplikacja gładzi. Tutaj zaczyna się właściwe działanie. Nałóż gładź równomiernie wzdłuż spoiny za pomocą pacy metalowej. Upewnij się, że cała przestrzeń spoiny jest dokładnie wypełniona masą. Trzymaj pacę pod kątem, który umożliwia dokładne wciśnięcie gładzi w szczelinę. To nie jest tylko smarowanie, to wypełnianie! Po nałożeniu pierwszej warstwy gładzi, należy ją przegładzić szeroką pacą ze stali nierdzewnej, aby uzyskać gładką powierzchnię. W przypadku spoin większych niż 3 mm, może być konieczne nałożenie kilku cieńszych warstw.
Krok czwarty – czas schnięcia. To moment na cierpliwość. Po nałożeniu gładzi, pozostaw ją do wyschnięcia i związania. Czas schnięcia zależy od grubości nałożonej warstwy, temperatury i wilgotności powietrza w pomieszczeniu. W przypadku większych nierówności lub głębszych spoin, może być konieczne nałożenie kolejnej cienkiej warstwy gładzi po całkowitym wyschnięciu warstwy wcześniejszej. Nie próbuj przyspieszać tego procesu za pomocą wentylatorów czy grzejników, może to prowadzić do zbyt szybkiego odparowania wody i powstawania pęknięć. Daj gładzi spokojnie "odetchnąć" i wyschnąć naturalnie.
Krok piąty – szlifowanie. Po całkowitym wyschnięciu ostatniej warstwy gładzi, czas na szlifowanie. Możesz szlifować ręcznie, używając bloczka do szlifowania z siatką lub papierem ściernym o odpowiedniej gradacji, lub mechanicznie, używając szlifierki do gipsu. Celem jest uzyskanie idealnie gładkiej powierzchni, niewidocznego przejścia między spoiną a płytą. Szlifowanie wymaga precyzji i delikatności. To jak wykańczanie mebla – szlifujesz, aż powierzchnia jest aksamitna w dotyku.
Krok szósty – czyszczenie narzędzi. Nie zapominaj o narzędziach. Po zakończeniu pracy, narzędzia należy oczyścić z resztek gładzi wodą. Zastygnięta gładź jest znacznie trudniejsza do usunięcia, więc zrób to od razu, zanim zastygnie na kamień.
Krok siódmy – dalsze prace. Po szlifowaniu powierzchnię należy dokładnie odpylić. Każdy drobny pyłek gipsu może być widoczny pod farbą. Możesz użyć odkurzacza lub wilgotnej (ale nie mokrej!) szmatki. Następnie zagruntuj całą powierzchnię ścian lub sufitu. Grunt wyrównuje chłonność podłoża i zapewnia lepszą przyczepność farby. Po wyschnięciu gruntu możesz przystąpić do malowania lub tapetowania. I voilà! Masz idealnie gładkie ściany gotowe na nowy rozdział w swoim wnętrzu.
Ważne wskazówki: Pamiętaj, że spoiny nie mogą być większe niż 3 mm przy spoinowaniu bez taśmy. Wypełnianie szczelin przy użyciu szpachelki powinno być precyzyjne. Po stwardnieniu pierwszej warstwy, nałożenie drugiej warstwy gładzi i wykończenie jej szeroką pacą jest niezbędne do uzyskania idealnego efektu. Przestrzeganie tych kroków pozwoli uniknąć wielu typowych błędów i zapewni trwałe i estetyczne wykończenie.
Spoinowanie bez taśmy vs z taśmą
Ach, ta kwestia, która budzi tyle dyskusji w świecie suchej zabudowy: spoinowanie z taśmą czy bez? Obie metody mają swoich zwolenników i przeciwników, a wybór zależy często od rodzaju używanej gładzi i preferencji wykonawcy. Weźmy na tapet gładź, o której rozmawiamy, czyli alabaster® FINISH CONNECT. Jak już wiemy, jest ona specjalnie przeznaczona do spoinowania płyt gipsowo-kartonowych bez konieczności stosowania taśmy. To jej wielki atut.
Spoinowanie bez taśmy, w przypadku gładzi do tego przeznaczonej, jest po prostu szybsze i prostsze. Eliminuje jeden z etapów prac, jakim jest wklejenie taśmy zbrojącej w warstwę gładzi. Zamiast tego, to sama gładź, dzięki zawartym w niej włóknom, przejmuje rolę zbrojenia. Włókna tworzą gęstą sieć wewnątrz spoiny, która zwiększa jej wytrzymałość na rozciąganie i zapobiega pękaniu. To tak, jakbyś miał wewnętrzny kręgosłup, który wzmacnia strukturę.
Kiedy spoinujesz bez taśmy, cały proces jest bardziej płynny. Nakładasz pierwszą warstwę, wypełniając spoinę, wygładzasz, czekasz na wyschnięcie, a następnie nakładasz drugą, wykańczającą warstwę. Nie musisz martwić się o równomierne zatopienie taśmy w gładzi czy o ewentualne pofałdowanie taśmy, co może się zdarzyć przy nieumiejętnym jej wklejeniu.
Spoinowanie z taśmą, historycznie rzecz biorąc, było standardową metodą spoinowania płyt gipsowo-kartonowych. Używano taśmy papierowej lub fizelinowej, którą zatapiano w pierwszej warstwie gładzi. Taśma ta miała za zadanie przejąć naprężenia, które mogą wystąpić w miejscach łączeń płyt, na przykład wskutek niewielkich ruchów konstrukcji budynku czy zmian temperatury i wilgotności. Taśma papierowa wymagała zazwyczaj wklejenia w mokrą gładź, co wymagało wprawy, aby uniknąć pęcherzy powietrza pod taśmą. Taśmy z siatki, często samoprzylepne, były nieco łatwiejsze w użyciu, ale ich skuteczność jako zbrojenia jest często mniejsza w porównaniu do taśm papierowych lub nowoczesnych gładzi z włóknami.
Decydując się na spoinowanie z taśmą, musisz liczyć się z dodatkowym czasem i materiałem. Sam koszt taśmy nie jest może ogromny, ale doliczając czas poświęcony na jej precyzyjne wklejenie i zatopienie, całość może potrwać nieco dłużej. W pewnych sytuacjach, na przykład przy spoinowaniu płyt w pomieszczeniach o podwyższonej wilgotności, stosowanie taśmy może być nadal zalecane, nawet przy użyciu gładzi z włóknami, dla dodatkowego wzmocnienia.
Główne zalety spoinowania bez taśmy to: szybsze wykonanie, łatwiejsza aplikacja (szczególnie dla osób mniej doświadczonych) i często płynniejszy proces wykańczania. Znika problem z ewentualnymi zgrubieniami pod taśmą czy jej widocznością po malowaniu, co czasami zdarzało się przy taśmach papierowych. To jakby przejść z tradycyjnego aparatu analogowego na cyfrowy – wiele rzeczy dzieje się szybciej i prościej.
Czy spoinowanie bez taśmy jest zawsze lepsze? Niekoniecznie. Wszystko zależy od specyfiki projektu, jakości gładzi oraz oczekiwań co do wytrzymałości spoiny. Nowoczesne gładzie z włóknami oferują wystarczającą wytrzymałość do standardowych zastosowań w suchej zabudowie. Jeśli jednak masz do czynienia z konstrukcją, która może być narażona na większe naprężenia, albo po prostu czujesz się pewniej, stosując tradycyjną metodę, spoinowanie z taśmą nadal jest validną opcją. To jak wybór między jazdą samochodem z manualną skrzynią biegów a automatem – oba dowiozą cię do celu, ale wrażenia z jazdy będą inne.
Warto pamiętać, że kluczowe jest stosowanie produktów zgodnie z przeznaczeniem i zaleceniami producenta. Jeśli producent gładzi wyraźnie wskazuje, że jest ona przeznaczona do spoinowania bez taśmy i spełnia odpowiednie normy wytrzymałościowe (np. typu 4A wg normy europejskiej), to można bez obaw ją tak stosować. Jeśli natomiast używasz tradycyjnej gładzi, stosowanie taśmy zbrojącej jest zazwyczaj niezbędne do zapewnienia trwałości połączenia.
Spoinowanie bez taśmy to krok w stronę uproszczenia procesu w suchej zabudowie. Daje szansę na szybsze ukończenie prac, bez kompromisów w kwestii jakości, pod warunkiem użycia odpowiedniego produktu. Ale jak w życiu, czasami warto znać i rozumieć metody tradycyjne, bo nigdy nie wiadomo, kiedy mogą się przydać, prawda?
Błędy przy spoinowaniu płyt GK i jak ich unikać
Nikt z nas nie jest nieomylny, a popełnianie błędów to część procesu uczenia się, zwłaszcza w pracach budowlanych. Przy spoinowaniu płyt GK lista potencjalnych pułapek jest długa, ale na szczęście większość z nich można uniknąć, stosując się do podstawowych zasad i zachowując ostrożność. Jak mawiają, przezorny zawsze ubezpieczony. Poznajmy najczęstsze grzechy główne spoinowania i sposoby na ich uniknięcie.
Pierwszy błąd to lekceważenie przygotowania podłoża. Montujesz płyty, spieszysz się, pomijasz fazowanie krawędzi ciętych, nie odkurzasz dokładnie, a już w ogóle zapominasz o gruntowaniu. A potem dziwisz się, że spoina pęka, albo gładź "odskakuje" od płyty. Podłoże musi być czyste, suche i stabilne. Sfazowanie krawędzi ciętych to konieczność, która tworzy miejsce na odpowiednią ilość gładzi. Odpylanie zapobiega tworzeniu się słabej warstwy między gładzią a płytą, a gruntowanie reguluje chłonność i poprawia przyczepność. To tak, jakbyś malował ściany bez umycia ich – farba może nie przylegać prawidłowo.
Drugi błąd, często spotykany, to nieprawidłowe przygotowanie gładzi. W przypadku gładzi gotowej do użycia, która ma idealną konsystencję prosto z wiadra, pokusa rozcieńczenia jej wodą, aby była bardziej plastyczna, jest duża. Nie ulegaj jej! Dodawanie wody do gładzi, która ma być stosowana bez taśmy, zmienia jej właściwości, osłabia jej wytrzymałość i może prowadzić do pęknięć spoiny po wyschnięciu. W przypadku gładzi sypkiej, problemem może być nieprawidłowe odmierzenie ilości wody, co skutkuje albo zbyt gęstą (trudną do aplikacji), albo zbyt rzadką (o słabych parametrach) masą. Zawsze mieszaj gładź zgodnie z instrukcją producenta, używając odpowiednich narzędzi, takich jak mieszadło koszykowe.
Trzeci błąd – zbyt cienka warstwa gładzi. Jeśli nałożysz za mało gładzi, szczególnie w spoinach bez taśmy, nie zapewnisz odpowiedniego zbrojenia wewnętrznego, a spoina będzie zbyt cienka, aby przenieść naprężenia. Może to skutkować pękaniem wzdłuż linii spoiny. Szczególnie dotyczy to spoin o krawędziach ciętych (sfazowanych), które wymagają pełnego wypełnienia na całej głębokości skosu. Nie bądź skąpy na gładzi tam, gdzie jej potrzeba.
Czwarty błąd – brak lub niewystarczająca liczba warstw. Spoinowanie, zwłaszcza bez taśmy, wymaga zazwyczaj nałożenia co najmniej dwóch warstw gładzi. Pierwsza warstwa wypełnia szczelinę, a druga warstwa, nałożona po wyschnięciu pierwszej, służy do wyrównania i uzyskania gładkiej powierzchni. Pomijanie drugiej warstwy lub nałożenie jej zbyt cienko może prowadzić do tego, że spoina będzie widoczna pod ostatecznym wykończeniem. To jakby malować ścianę tylko jedną warstwą farby – efekt będzie daleki od ideału.
Piąty błąd – szpachlowanie zbyt dużych szczelin. Nowoczesne gładzie do spoinowania bez taśmy są zazwyczaj przeznaczone do szczelin o szerokości maksymalnie 3 mm. Jeśli masz większe szczeliny, np. w wyniku niedokładnego montażu płyt, spoinowanie bez taśmy może być niewystarczające. W takich przypadkach lepszym rozwiązaniem może być zastosowanie taśmy zbrojącej lub użycie innego rodzaju masy szpachlowej, przeznaczonej do większych ubytków, przed przystąpieniem do spoinowania właściwą gładzią. Ignorowanie tego limitu to prosta droga do pęknięć.
Szósty błąd – praca w nieodpowiednich warunkach temperaturowych. Gładzie, podobnie jak wiele innych materiałów budowlanych, mają zalecany zakres temperatur do aplikacji i schnięcia. Zazwyczaj jest to od +10°C do +25°C. Praca w zbyt niskiej temperaturze może spowolnić lub nawet zatrzymać proces wiązania i schnięcia. Zbyt wysoka temperatura, zwłaszcza w połączeniu z niską wilgotnością, może powodować zbyt szybkie schnięcie gładzi, co zwiększa ryzyko skurczu i pęknięć. To trochę jak próba gotowania obiadu na mrozie albo na pustyni – warunki są po prostu niesprzyjające.
Siódmy błąd – nieodpowiednie szlifowanie. Zbyt wczesne szlifowanie gładzi, gdy jeszcze nie wyschła całkowicie, prowadzi do mazania się materiału i trudności w uzyskaniu gładkiej powierzchni. Z kolei zbyt intensywne szlifowanie może prowadzić do przeszlifowania i uszkodzenia powierzchni gładzi lub nawet samej płyty GK. Używanie papieru ściernego o zbyt grubej gradacji pozostawi widoczne rysy. Cierpliwość jest kluczowa – poczekaj, aż gładź wyschnie na kamień, a następnie szlifuj delikatnie, używając drobniejszej gradacji papieru, np. P180 lub P220, a do wygładzenia nawet P240 lub drobniejszy.
Ósmy błąd – zaniechanie odpylenia przed gruntowaniem i malowaniem. Po szlifowaniu powstaje mnóstwo drobnego pyłu gipsowego. Jeśli nie usuniesz go dokładnie, utworzy on słabą warstwę między gładzią a gruntem lub farbą. Skutek? Słaba przyczepność powłok wykończeniowych, łuszczenie się farby, a nawet widoczne grudki na powierzchni. To jak próba klejenia czegoś do zakurzonej powierzchni – nie będzie się trzymać.
Dziewiąty błąd – użycie nieodpowiedniego narzędzia do aplikacji. Zamiast pacy metalowej o odpowiedniej szerokości, używasz czegoś przypadkowego, co jest pod ręką. W efekcie gładź jest nałożona nierównomiernie, a jej wygładzenie jest utrudnione. Paca metalowa pozwala na precyzyjne wciśnięcie gładzi w spoinę i jej gładkie rozprowadzenie. Odpowiednie narzędzia to połowa sukcesu.
Dziesiąty błąd – niecierpliwość. Cały proces spoinowania, od przygotowania po szlifowanie i gruntowanie, wymaga czasu i cierpliwości. Każdy etap ma swoje tempo. Próba przyspieszenia któregokolwiek z nich, np. przez nakładanie kolejnej warstwy gładzi na mokrą jeszcze warstwę poprzednią, skończy się katastrofą. Daj sobie i materiałom czas. To jak nauka języka – wymaga regularności i cierpliwości, żeby osiągnąć płynność.
Pamiętaj, że kluczem do uniknięcia błędów jest przestrzeganie instrukcji producenta gładzi, staranne przygotowanie podłoża, odpowiednia aplikacja w co najmniej dwóch warstwach (jeśli wymaga tego produkt), cierpliwość podczas schnięcia i dokładne szlifowanie oraz odpylanie. Choć może się wydawać, że to dużo drobiazgów, każdy z nich ma znaczenie dla ostatecznego efektu – gładkiej i trwałej powierzchni.
Q&A
Czym jest gładź do spoinowania płyt GK?
Gładź do spoinowania płyt GK to specjalistyczny materiał budowlany używany do wypełniania i wygładzania szczelin oraz łączeń pomiędzy płytami gipsowo-kartonowymi, tworząc jednolitą i gładką powierzchnię ścian i sufitów, przygotowaną do dalszego malowania lub tapetowania.
Czy muszę używać taśmy do spoinowania płyt GK?
To zależy od rodzaju użytej gładzi. Nowoczesne gładzie, jak np. te zawierające włókna fibrylizowane (alabaster® FINISH CONNECT), są przeznaczone do spoinowania bez konieczności stosowania taśmy, oferując odpowiednią wytrzymałość spoiny dzięki wewnętrznemu zbrojeniu.
Jakie błędy najczęściej popełnia się przy spoinowaniu płyt GK?
Najczęstsze błędy to niedostateczne przygotowanie podłoża (brak odpylenia, gruntowania), nieprawidłowe przygotowanie gładzi (np. rozcieńczanie gładzi gotowej do użycia), nakładanie zbyt cienkich warstw, praca w nieodpowiednich warunkach temperaturowych, nieprawidłowe szlifowanie oraz zaniechanie odpylenia przed gruntowaniem i malowaniem.
Jak przygotować podłoże przed spoinowaniem płyt GK?
Podłoże powinno być czyste, suche i stabilnie zamocowane. Krawędzie cięte płyt należy sfazować, a następnie całość dokładnie odpylić i zagruntować odpowiednim gruntem.
Jak długo schnie gładź do spoinowania płyt GK?
Czas schnięcia gładzi zależy od wielu czynników, takich jak grubość nałożonej warstwy, temperatura i wilgotność powietrza w pomieszczeniu. Zazwyczaj wynosi od kilku do kilkunastu godzin, ale zawsze należy sprawdzić zalecenia producenta na opakowaniu produktu.