Jaka płyta OSB na ścianę? Wybierz najlepszą w 2025
W gąszczu dostępnych materiałów budowlanych, decyzja o wyborze odpowiedniej płyty na poszycie ścian to moment, który wielu inwestorów i wykonawców poddaje głębszej refleksji. Gdy pojawia się pytanie, Jaka płyta OSB na ścianę będzie najlepszym wyborem, kluczowa odpowiedź to najczęściej płyta OSB/3, doceniana za jej wszechstronność i podwyższoną odporność na działanie wilgoci, co czyni ją uniwersalnym rozwiązaniem zarówno wewnątrz, jak i w pewnych zastosowaniach zewnętrznych.
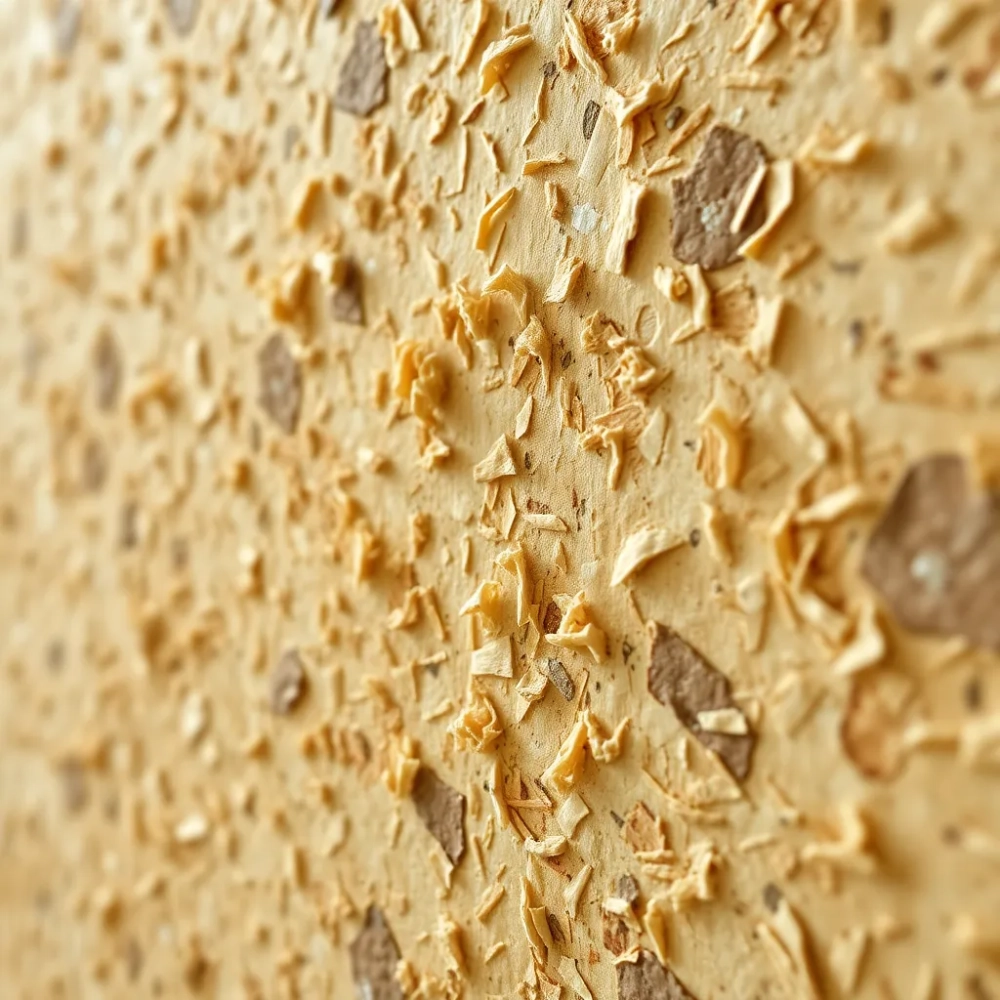
Typ Płyty OSB | Główne Przeznaczenie i Warunki Stosowania | Orientacyjna Odporność na Wilgoć* | Typowe Zastosowanie w Kontekście Ścian | Przydatność dla Ścian (Ogólnie) |
---|---|---|---|---|
OSB/1 | Zastosowania wewnątrz budynków w suchych warunkach. Nieprzystosowane do przenoszenia obciążeń. | Bardzo niska | Nie nadaje się do ścian konstrukcyjnych. Możliwe użycie w elementach dekoracyjnych w suchych wnętrzach. | Niska (ograniczona tylko do suchych, nieobciążonych elementów wewnętrznych) |
OSB/2 | Zastosowania wewnątrz budynków w suchych warunkach, ale wymagające przenoszenia obciążeń. | Niska | Ściany wewnętrzne nośne i działowe w suchych pomieszczeniach, jako poszycie zapewniające sztywność. | Umiarkowana (dobra do wnętrz suchych, ale tylko tam) |
OSB/3 | Zastosowania w warunkach umiarkowanej wilgotności, zarówno wewnątrz, jak i na zewnątrz (wymaga dodatkowego zabezpieczenia). Przystosowana do przenoszenia obciążeń. | Umiarkowana do dobra (dzięki lepiszczu, ale nie wodoszczelna) | Poszycia ścian zewnętrznych jako usztywnienie konstrukcji i podkład pod elewację/izolację. Ściany wewnętrzne w pomieszczeniach o podwyższonej wilgotności (kuchnie, łazienki). | Wysoka (uniwersalna) |
OSB/4 | Zastosowania w warunkach podwyższonej wilgotności, wymagające przenoszenia dużych obciążeń. | Wysoka | Rzadziej stosowana w typowych ścianach jednorodzinnych, głównie w obiektach przemysłowych, halach. | Bardzo wysoka (ale często przerost formy nad treścią dla standardowych zastosowań) |
*Odporność na wilgoć oznacza mniejsze pęcznienie i zachowanie części wytrzymałości w warunkach podwyższonej wilgotności, nie wodoszczelność ani możliwość ciągłego kontaktu z wodą.
Widzimy wyraźnie, że klasyfikacja według norm europejskich nie jest przypadkowa i stanowi drogowskaz dla każdego, kto podchodzi do tematu z należytą starannością. Każdy typ płyty OSB został stworzony z myślą o innych wyzwaniach, a ignorowanie tych różnic to prosta droga do problemów, takich jak deformacja czy utrata wytrzymałości w nieodpowiednim środowisku. Wybór OSB/3 jako domyślnego, bazowego rozwiązania dla większości typów ścian w budownictwie mieszkaniowym ma głęboki sens praktyczny i jest rekomendowany przez specjalistów.Jaka grubość płyty OSB będzie odpowiednia na ścianę?
Wybór grubości płyty OSB na ścianę to niczym dobór odpowiedniego garnituru – musi być dopasowany do sytuacji i pełnić swoją rolę bez zarzutu.
To nie jest jedna odpowiedź dla wszystkich, lecz decyzja zależna od szeregu czynników inżynierskich i funkcjonalnych, które często są niedoceniane.
Stojąc przed regałem w markecie budowlanym lub analizując kosztorysy, widzimy płyty o grubościach od kilku do ponad dwudziestu milimetrów, ale które z nich nadają się na ściany i dlaczego właśnie te?
Pierwszym i najważniejszym kryterium jest rola, jaką ściana ma pełnić w konstrukcji budynku.
Czy będzie to ściana nośna, przejmująca obciążenia z dachu lub stropów, czy może lekka ściana działowa, której głównym zadaniem jest oddzielenie pomieszczeń?
W przypadku ścian działowych, które nie przenoszą znaczących obciążeń konstrukcyjnych, często stosuje się płyty OSB o grubości 10 mm lub 12 mm.
Te grubości zapewniają wystarczającą sztywność dla konstrukcji, stanowią solidne podłoże do montażu płyt gipsowo-kartonowych, paneli ściennych czy nawet bezpośredniego malowania (po odpowiednim przygotowaniu powierzchni).
Płyta 10 mm jest lżejsza i tańsza, ale 12 mm oferuje już zauważalnie większą wytrzymałość i lepszą odporność na punktowe uderzenia czy obciążenia związane z wieszaniem szafek, półek czy telewizorów.
Kiedy mówimy o ścianach nośnych lub ścianach zewnętrznych, które oprócz przenoszenia obciążeń wertykalnych, pełnią także funkcję usztywnienia konstrukcji w płaszczyźnie poziomej (tzw. tarcza ścienna, odporna na wiatr czy drgania sejsmiczne), wymagania co do grubości znacząco rosną.
Tutaj standardem, a często minimum wymaganym przez normy budowlane i projekty konstrukcyjne, jest płyta OSB/3 o grubości 15 mm, a jeszcze lepiej 18 mm.
Taka grubość, w połączeniu z odpowiednim rozstawem słupków konstrukcyjnych (zazwyczaj co 400 mm lub 600 mm) i prawidłowym schematem mocowania (specjalistyczne gwoździe pierścieniowe lub wkręty w ściśle określonym rozstawie wzdłuż krawędzi płyty i na słupkach pośrednich), gwarantuje, że ściana sprosta stawianym jej wymaganiom statycznym.
Płyta 18 mm oferuje znacznie większą odporność na ścinanie i zginanie w porównaniu do cieńszych odpowiedników, co jest kluczowe dla stabilności całego budynku, zwłaszcza w domach o konstrukcji szkieletowej.
W przypadku ścian zewnętrznych, grubość płyty ma także wpływ na możliwość przenoszenia obciążeń od warstw zewnętrznych, takich jak system ocieplenia i elewacji.
Grubsza płyta (15-18 mm) stanowi pewniejsze podłoże dla mocowań mechanicznych, co jest istotne przy cięższych systemach elewacyjnych.
Cienkie płyty, np. 12 mm, stosowane na zewnątrz wymagają zazwyczaj gęstszego rozstawu słupków (np. 400 mm) lub zastosowania dodatkowych usztywnień i są raczej kompromisem niż optymalnym wyborem dla solidnej, trwałej przegrody zewnętrznej.
Niektórzy eksperci z branży twierdzą, że szukanie oszczędności na grubości płyty OSB na ścianę zewnętrzną to „granie na nosie” własnemu bezpieczeństwu i przyszłym kosztom napraw.
Co ciekawe, w przypadku dachów, gdzie obciążenia śniegiem i wiatrem bywają znaczące, często stosuje się płyty o grubości 22 mm, a nawet 25 mm, zwłaszcza przy większych rozstawach krokwi.
Ten przykład pokazuje skalę, z jaką rośnie zapotrzebowanie na wytrzymałość materiału wraz ze wzrostem obciążeń i rozpiętości konstrukcji.
Choć ściany przenoszą obciążenia w inny sposób, analogia do sztywności dachu jest pouczająca i podkreśla znaczenie grubości płyty w przenoszeniu obciążeń i zapewnianiu stabilności.
Analizując koszty, widzimy wyraźnie trend wzrostu ceny wraz z grubością. Przykładowo, jeśli płyta OSB/3 12 mm kosztuje około 40-50 zł/m², to za płytę 15 mm zapłacimy już w okolicach 48-60 zł/m², a za 18 mm nawet 55-70 zł/m² (są to ceny orientacyjne, zróżnicowane w zależności od producenta i regionu).
Różnica 10-20 zł na metrze kwadratowym może wydawać się duża przy budowie całego domu, ale w kontekście całkowitego kosztu inwestycji, dopłacenie kilku tysięcy złotych za grubsze, solidniejsze poszycie ścian nośnych i zewnętrznych to inwestycja w spokój i trwałość na lata.
Lżejsze płyty są łatwiejsze w transporcie i montażu, co jest plusem dla wykonawców, ale ich parametry techniczne mogą okazać się niewystarczające dla bardziej wymagających aplikacji.
Waga płyty OSB 12 mm to około 8 kg/m², 15 mm to około 10 kg/m², a 18 mm to już około 12 kg/m².
Różnica w ciężarze ma znaczenie przy logistyce na budowie i samej pracy, ale nie może być głównym wyznacznikiem wyboru grubości.
Ważnym aspektem, często pomijanym w dyskusji o grubości, jest sposób mocowania płyty do konstrukcji drewnianej.
Grubsza płyta pozwala na zastosowanie dłuższych wkrętów lub gwoździ, co zwiększa siłę połączenia i tym samym nośność całej tarczy ściennej.
Standardowo stosuje się wkręty do drewna lub gwoździe o długości co najmniej 2,5-krotności grubości płyty, przy czym minimalna długość zakotwienia w drewnie konstrukcyjnym powinna wynosić np. 40-50 mm.
Dla płyty 18 mm potrzebne są zatem wkręty o długości min. ok. 45 mm, ale lepiej użyć 50 mm lub 60 mm, aby zapewnić solidne trzymanie, zwłaszcza na obciążonych krawędziach.
Prawidłowe gęste rozstawienie łączników na krawędziach płyt (np. co 150 mm) i rzadsze w środku płyty (np. co 300 mm) jest absolutnie krytyczne dla uzyskania założonej wytrzymałości ściany.
Instrukcje producentów płyt oraz wytyczne projektowe muszą być tutaj bezwzględnie przestrzegane, ponieważ błędy w mocowaniu mogą zniweczyć nawet zastosowanie najgrubszej i najbardziej wytrzymałej płyty.
Wyobraź sobie taką sytuację: projektant policzył, że ściana z płyty 15 mm zapewni stabilność przy danym rozstawie słupków, ale wykonawca oszczędził na łącznikach, mocując je rzadziej.
Efekt? Ściana może nie spełnić wymagań i być podatna na deformacje czy, w skrajnych przypadkach, nawet utratę nośności pod wpływem silnego wiatru czy obciążeń stropu.
To klasyczny przykład, gdzie teoretyczna wytrzymałość materiału nie przekłada się na realną wytrzymałość konstrukcji z powodu błędów wykonawczych.
Podsumowując rozważania o grubości, zasada jest prosta, choć jej zastosowanie wymaga analizy specyfiki projektu.
Na ściany działowe i inne niekonstrukcyjne elementy wewnętrzne zazwyczaj wystarczy 10-12 mm.
Na konstrukcji ścian nośnych i ścian zewnętrznych stosuj płyty OSB/3 o grubości 15 mm lub 18 mm, pamiętając, że 18 mm oferuje znacznie większy margines bezpieczeństwa i pewność konstrukcji.
Zawsze weryfikuj wymagania projektowe i lokalne przepisy budowlane, które mogą precyzować minimalne dopuszczalne grubości w zależności od strefy obciążenia wiatrem, wysokości budynku czy innych czynników.
Dopłacenie do grubszej płyty tam, gdzie jest to konstrukcyjnie uzasadnione, to decyzja, której nigdy nie pożałujesz, zapewniając swojemu domowi solidne fundamenty dosłownie i w przenośni.
Krawędzie płyt OSB: Proste czy pióro-wpust do montażu na ścianie?
Wybór typu krawędzi płyty OSB, podobnie jak grubość, wpływa znacząco na proces montażu, szczelność konstrukcji i w pewnym stopniu na jej wytrzymałość.
Masz do wyboru zasadniczo dwa rodzaje: płyty z prostymi krawędziami (tzw. Square Edge - SE) oraz płyty z systemem pióro-wpust (Tongue and Groove - T&G).
Choć na pierwszy rzut oka różnica wydaje się niewielka, w praktyce ma ona kolosalne znaczenie, zwłaszcza gdy celem jest stworzenie ściany o wysokiej szczelności i spójności konstrukcyjnej.
Płyty z prostymi krawędziami są najprostsze w produkcji, a co za tym idzie – zazwyczaj najtańsze.
Ich główną zaletą jest łatwość cięcia i dopasowania, co jest przydatne zwłaszcza przy obróbce otworów okiennych i drzwiowych, narożników czy skosów.
Przy montażu płyt SE na ścianie, każda krawędź płyty, w której stykają się dwa panele, musi być podparta przez element konstrukcyjny – słup lub rygel.
Oznacza to, że rozstaw słupków musi być dostosowany do szerokości płyty, tak aby styki wypadały dokładnie na ich środku.
Jednym z kluczowych aspektów stosowania płyt SE na ścianach, zwłaszcza zewnętrznych, jest konieczność pozostawienia szczelin dylatacyjnych o szerokości około 3 mm pomiędzy sąsiadującymi panelami.
Drewnopochodne materiały, jak OSB, reagują na zmiany wilgotności powietrza, pęczniejąc lub kurcząc się.
Pozostawienie tych szczelin minimalizuje ryzyko naprężeń i deformacji całej tarczy ściennej.
Te szczeliny, choć konieczne, stanowią potencjalne mostki powietrzne i miejsca, przez które może przedostawać się wilgoć (jeśli brakuje odpowiedniego zabezpieczenia zewnętrznego).
Dlatego też, w przypadku ścian zewnętrznych, konieczne jest solidne zaklejenie wszystkich spoin między płytami specjalistyczną taśmą, która zapewni szczelność powietrzną poszycia.
Z drugiej strony mamy płyty z systemem pióro-wpust.
Charakteryzują się one specjalnie frezowanymi krawędziami, gdzie jedna strona posiada "pióro" (wypust), a druga "wpust" (rowek), które zazębiają się ze sobą podczas montażu.
Główną przewagą płyt T&G, zwłaszcza w kontekście konstrukcji ścian zewnętrznych i nośnych, jest możliwość tworzenia połączeń między panelami, które nie wymagają bezwzględnego podparcia na słupku.
Chociaż wciąż zaleca się, aby większość połączeń krawędziowych (zwłaszcza krótkie krawędzie płyt, tzw. czoła) wypadała na elementach konstrukcji nośnej, system pióro-wpust pozwala na "wiązanie" paneli między słupkami.
System T&G tworzy sztywniejsze i bardziej ciągłe połączenie między płytami, co poprawia właściwości nośne i sztywność tarczy ściennej.
Co więcej, zazębione krawędzie pióro-wpust znacząco redukują przenikanie powietrza przez styki płyt, tworząc naturalnie szczelniejsze poszycie już na etapie montażu OSB.
To kluczowa zaleta, gdy celem jest budowa domu energooszczędnego lub pasywnego, gdzie szczelność przegród zewnętrznych ma fundamentalne znaczenie.
Przy zastosowaniu pióro-wpustu, konieczność skrupulatnego taśmowania wszystkich spoin jest mniejsza (choć często wciąż zalecana, aby uzyskać absolutną szczelność na poziomie standardów pasywnych), co może przyspieszyć prace.
Jednak płyty T&G nie są pozbawione wad.
Są zazwyczaj droższe od płyt z prostymi krawędziami, a frezowane krawędzie są bardziej podatne na uszkodzenia podczas transportu i przenoszenia, co może generować odpad.
Cięcie płyt T&G do niestandardowych rozmiarów oznacza utratę systemu pióro-wpust na krawędzi cięcia, co w danym miejscu wymusza traktowanie połączenia jak w przypadku płyty SE – wymaga podparcia i zabezpieczenia szczeliny.
Montaż pióro-wpust wymaga także nieco większej precyzji i delikatności przy zbijaniu paneli, aby nie uszkodzić frezów.
Mimo że system tworzy "ciasne" połączenie, producenci nadal zalecają pozostawienie niewielkich szczelin dylatacyjnych na obwodzie całej ściany (np. przy połączeniu ze stropem czy innymi ścianami), aby uwzględnić ruchy drewna.
Porównując te dwa rozwiązania w kontekście montażu płyty OSB na ścianie, widzimy wyraźny podział w preferencjach.
Płyty SE są często wybierane do ścian wewnętrznych, gdzie wymagania dotyczące szczelności są niższe, a łatwość dopasowania przy licznych wewnętrznych narożnikach czy ościeżach jest cenną zaletą.
Są też wyborem bardziej ekonomicznym dla prostych, mniej wymagających konstrukcji.
Natomiast system pióro-wpust dla lepszej szczelności i spójności konstrukcyjnej jest zdecydowanie preferowany, a często wręcz zalecany, do poszyć ścian zewnętrznych w budownictwie szkieletowym.
Choć materialnie droższy, może zaoferować oszczędności w czasie pracy ekipy budowlanej i, co ważniejsze, przyczynia się do lepszych parametrów energetycznych budynku dzięki redukcji niekontrolowanej infiltracji powietrza.
Wyobraź sobie walkę o każdy wat ciepła w domu niskoenergetycznym; nieszczelności w poszyciu z płyt SE, nawet starannie taśmowane, zawsze niosą większe ryzyko niż naturalnie doszczelnione połączenia pióro-wpust.
To trochę jak porównanie ręcznie szytej, impregnowanej plandeki do nowoczesnej membrany paroprzepuszczalnej - obie mogą chronić, ale skuteczność i trwałość bywają radykalnie różne.
Istnieją szacunki dotyczące czasu montażu, choć są one bardzo zmienne i zależą od doświadczenia ekipy, skomplikowania projektu czy wielkości płyt.
Niemniej jednak, niektórzy specjaliści uważają, że na dużych, prostych powierzchniach ścian zewnętrznych, zastosowanie płyt T&G może przyspieszyć montaż nawet o 10-15% w porównaniu do płyt SE z koniecznością precyzyjnego podparcia każdej krawędzi i późniejszego skrupulatnego taśmowania.
Dla przykładu, montaż 50 m² ściany poszytej płytą OSB SE może zająć 9-10 roboczogodzin (wliczając czas na cięcie, dopasowanie, mocowanie i podstawowe uszczelnienie szczelin taśmą budowlaną), podczas gdy ten sam metraż z płyt T&G może pochłonąć 8-9 roboczogodzin, zapewniając przy tym lepszy efekt szczelności bazowej przed nałożeniem membrany.
Szczególnie widoczne jest to na długich krawędziach płyt, gdzie połączenie pióro-wpust tworzy stabilne połączenie między słupkami, co redukuje potrzebę stosowania dodatkowego deskowania czy łat w celu podparcia spoin (choć dobre praktyki nadal zalecają pewne wsparcie, np. blocking).
Ten aspekt doboru krawędzi wpływa na czas i jakość montażu w sposób, który warto uwzględnić w planowaniu inwestycji.
Płyta T&G o grubości 15 mm lub 18 mm na krawędziach 4-stronnych (powszechnie dostępna) to rozwiązanie premium dla ścian zewnętrznych i dachów, oferujące maksymalną stabilność, sztywność i bazową szczelność powietrzną.
Dla ścian wewnętrznych i budżetowych rozwiązań na zewnątrz (pod warunkiem bezwzględnego przestrzegania reżimu taśmowania spoin i zastosowania odpowiedniej membrany), płyty SE o grubości 12 mm lub 15 mm mogą być wystarczające.
Ostateczny wybór powinien być podyktowany nie tylko ceną zakupu samego materiału, ale także kosztami pracy, wymaganiami dotyczącymi parametrów energetycznych budynku oraz przeznaczeniem ściany.
Nie ma złych krawędzi per se, są tylko krawędzie niewłaściwie dobrane do zadania.
Podsumowując, jeśli budujesz na lata, z naciskiem na energooszczędność i trwałość, system pióro-wpust na 4-stronach płyt OSB/3 15-18 mm jest wyborem, który da Ci pewność solidnej bazy pod dalsze warstwy ściany zewnętrznej.
Wodoodporność płyt OSB a zastosowanie w ścianach zewnętrznych i wewnętrznych
Wokół tematu wodoodporności płyt OSB narosło wiele mitów i nieporozumień.
Często słyszy się, że płyta OSB jest "wodoodporna", co jest półprawdą, która w praktyce budowlanej może prowadzić do poważnych problemów.
Kluczowe jest zrozumienie, że płyty OSB, nawet te najwyższej klasy, nie są wodoszczelne i nie mogą stanowić samodzielnej bariery hydroizolacyjnej w przegrodzie budowlanej.
Ich "wodoodporność" odnosi się raczej do ograniczonej nasiąkliwości i lepszego zachowania parametrów mechanicznych w warunkach podwyższonej wilgotności powietrza w porównaniu do innych materiałów drewnopochodnych.
Płyty OSB produkowane są poprzez sprasowanie odpowiednio wyselekcjonowanych wiórów drewna, które są połączone ze sobą za pomocą żywic syntetycznych pod wysokim ciśnieniem i w wysokiej temperaturze.
To właśnie rodzaj i ilość zastosowanego lepiszcza decyduje o stopniu odporności na wilgoć OSB/3 nie oznacza wodoodporności, a jedynie redukcję chłonności i pęcznienia.
Płyty OSB/1 i OSB/2 wykorzystują zazwyczaj mniej odporne na wodę żywice (np. na bazie mocznika), przez co nadają się wyłącznie do suchych pomieszczeń wewnętrznych (klasa użytkowania 1 według Eurokodu 5).
Płyty OSB/3 i OSB/4 produkowane są z użyciem bardziej odpornych żywic, takich jak kleje melaminowo-mocznikowo-formaldehydowe (MUPF) lub, co coraz częstsze, izocyjanianowe kleje poliuretanowe (PMDI) lub fenolowe (PF).
Te bardziej odporne żywice otaczają wióry drewna, utrudniając wchłanianie wody.
Jednak samo drewno, nawet "zalakowane" żywicą, wciąż jest materiałem higroskopijnym i będzie wchłaniać wilgoć z otoczenia.
W standardowych testach (np. immersja w wodzie przez 24 godziny), płyty OSB/3 wykazują znacznie mniejsze pęcznienie (np. rzędu 12-15% grubości) w porównaniu do płyt OSB/2 (które mogą napęcznieć powyżej 20%), a także lepiej zachowują swoją wytrzymałość na zginanie w stanie wilgotnym.
Ale te testy to symulacja skrajnych warunków; w praktyce kluczowe jest długotrwałe narażenie na wilgoć lub, co gorsza, na bezpośrednie działanie wody opadowej czy nieszczelności instalacji.
W przypadku ścian zewnętrznych, stosowanie płyt OSB/3 jako poszycia konstrukcyjnego jest standardem, ale nie oznacza, że płyta może być narażona na deszcz i śnieg bez ochrony.
OSB/3 pełni rolę usztywnienia konstrukcji i warstwy przenoszącej obciążenia, ale przede wszystkim stanowi bazę dla systemów ochrony przed wodą i wiatrem oraz dla izolacji i elewacji.
Bezwzględnie konieczne jest zabezpieczenie zewnętrznej strony płyty przed wodą opadową i wiatrem za pomocą specjalnej membrany fasadowej (paroprzepuszczalnej, tzw. wiatroizolacji).
Membrana ta układa się na poszyciu OSB, zazwyczaj z zakładami uszczelnianymi taśmą, i ma za zadanie odprowadzać wodę, która mogłaby przedostać się przez szczeliny elewacji czy nieszczelności, jednocześnie umożliwiając "oddychanie" ściany, czyli dyfuzję pary wodnej z wnętrza budynku na zewnątrz.
Pominięcie lub niewłaściwe zamontowanie membrany prowadzi prostą drogą do zawilgocenia płyty OSB, a w konsekwencji do jej trwałego uszkodzenia, pęcznienia, utraty nośności i rozwoju pleśni czy grzybów.
Szczególną uwagę należy zwrócić na krawędzie płyt OSB, zwłaszcza te cięte, np. przy oknach i drzwiach.
Fabryczne krawędzie (z piórem i wpustem) mają lepszą odporność na wilgoć, ale krawędzie cięte wchłaniają wodę znacznie łatwiej.
W dobrych praktykach budowlanych zaleca się zabezpieczanie takich krawędzi, np. specjalnymi farbami krawędziowymi do drewna lub szczelne oklejanie ich taśmami systemowymi stosowanymi do membran i paroizolacji.
Pozwala to zminimalizować ryzyko punktowego wnikania wody, np. wokół ościeżnic okiennych czy w dolnej części ściany, gdzie może gromadzić się wilgoć od gruntu.
Wyobraź sobie sytuację: świetnie zbudowany szkielet, ściana poszyta grubym OSB/3, membrana fasadowa położona perfekcyjnie na dużej powierzchni, ale... wokół jednego okna krawędzie cięte płyt OSB nie zostały zabezpieczone.
Mały przeciek przy parapecie podczas ulewnego deszczu lub nieszczelność taśmy okiennej w tym miejscu przez miesiące doprowadza do lokalnego zawilgocenia i pęcznienia płyty dokładnie tam, gdzie nikt się tego nie spodziewał, skutkując koniecznością poważnych napraw fasady w przyszłości.
Wewnątrz budynku, gdzie wilgotność jest zazwyczaj niższa i kontrolowana, zastosowanie płyt OSB/2 w suchych pomieszczeniach (salon, sypialnie) jest wystarczające i ekonomiczne.
Jednak w pomieszczeniach o podwyższonej wilgotności, takich jak kuchnie, łazienki czy pralnie, rekomendowane jest użycie płyt OSB/3.
Nawet w takich warunkach, jeśli płyta ma stanowić podkład pod płytki ceramiczne, zwłaszcza w strefach mokrych (np. prysznic, okolice wanny, ściana za zlewem w kuchni), hydroizolacja w wilgotnych wnętrzach, nawet z OSB/3 jest absolutnie niezbędna.
Oznacza to nałożenie na powierzchnię płyty specjalnych folii w płynie, mas hydroizolacyjnych czy mat uszczelniających przed położeniem płytek.
Płyta OSB/3 pod płytkami w łazience jest dobrym, stabilnym podkładem, ale nie zapewnia sama w sobie bariery dla wody – to zadanie dla warstwy hydroizolacji na niej wykonanej.
Ignorowanie tej zasady, np. kładzenie płytek bezpośrednio na niezabezpieczonej hydroizolacją płycie OSB w prysznicu, gwarantuje, że w krótkim czasie woda przedostanie się do płyty, spowoduje jej zniszczenie i będzie prowadzić do zawilgocenia i pleśnienia całej ściany.
Płyty OSB, zwłaszcza OSB/3, są odporne na krótkotrwałe, przypadkowe zawilgocenie podczas budowy (np. kilkudniowe opady przed założeniem membrany dachowej czy ściennej), o ile mają szansę szybko wyschnąć.
Dłuższe zalanie lub permanentne narażenie na wilgoć (np. od nieszczelnego okna, dachu, instalacji) nieuchronnie prowadzi do problemów, niezależnie od typu płyty.
Dlatego prawidłowe wykonanie pozostałych warstw przegrody – szczelnego dachu, właściwego odwodnienia opadowego, solidnej hydroizolacji fundamentów, precyzyjnego montażu okien i drzwi z uszczelnieniem zewnętrznym i wewnętrznym, a także zapewnienie odpowiedniej wentylacji wewnątrz budynku – ma kluczowe znaczenie dla długowieczności poszycia z płyt OSB.
OSB/3 do ścian zewnętrznych to świetny wybór, ale nie zapominajmy o jej towarzyszach: membranie fasadowej, listwach dystansowych tworzących pustkę wentylacyjną i dobrze wykonanej elewacji.
Te elementy razem tworzą system, który chroni OSB i całą ścianę przed zgubnym działaniem wody i wilgoci z zewnątrz, a od wewnątrz przed nadmierną parą wodną za pomocą folii paroizolacyjnej (w chłodniejszych strefach klimatycznych).
Dane dotyczące pęcznienia płyt OSB/3 po długotrwałym narażeniu na wysoką wilgotność powietrza (>85%) lub po teście cyklicznej wilgotności (zmiany wilgotności i temperatury) wciąż pokazują pewien poziom pęcznienia i utraty wytrzymałości, choć znacząco mniejszy niż w przypadku OSB/1 i OSB/2.
To naukowy dowód na to, że nawet najbardziej "odporne" płyty OSB wymagają przemyślanego projektowania i prawidłowego wykonania w kontakcie z wodą i długotrwałą wilgocią.
Pamiętaj, że choć płyta OSB/3 jest zaprojektowana do pracy w warunkach umiarkowanej wilgotności, jej "wodoodporność" jest cechą techniczną mającą zapobiegać SZYBKIEMU zniszczeniu, a nie wieczną gwarancją przed skutkami zanurzenia czy stałego zamoczenia.
Zatem, stosowanie płyt OSB na ścianach zewnętrznych bez odpowiedniej membrany, z niezabezpieczonymi krawędziami, czy używanie płyt OSB/1 lub OSB/2 w łazienkach bez hydroizolacji to przepisy na katastrofę.
Prawidłowe użycie płyty OSB/3, w połączeniu z adekwatnymi warstwami zabezpieczającymi i wentylacyjnymi w ścianie zewnętrznej oraz z hydroizolacją w strefach mokrych we wnętrzach, to klucz do trwałej i zdrowej konstrukcji.
Jak już wspomnieliśmy w części dotyczącej krawędzi, czasami liczy się także czas montażu. Przyjrzyjmy się szacunkowemu porównaniu czasu potrzebnego na montaż poszycia ścian dla płyt z prostymi krawędziami i systemem pióro-wpust. Dane te są uproszczeniem, ale ilustrują potencjalne różnice.
- Montaż poszycia z płyt OSB/3 na standardowej ścianie o powierzchni 50 m²:
- Przygotowanie materiału i konstrukcji: ok. 60 min
- Płyty SE (proste krawędzie): Czas na cięcie i dopasowanie paneli: 180 min; Czas na mocowanie paneli do konstrukcji: 240 min; Czas na skrupulatne uszczelnianie spoin taśmą: 120 min; Całkowity czas (szacunkowo): 60 + 180 + 240 + 120 = 600 minut (10 godzin)
- Płyty T&G (pióro-wpust): Czas na cięcie i dopasowanie paneli: 200 min (nieco bardziej wymagające dopasowanie frezów i mniejsza elastyczność przy cięciu); Czas na mocowanie paneli do konstrukcji: 220 min (potencjalnie szybsze dzięki łatwiejszemu wyrównaniu); Czas na dodatkowe mocowania na spoinach między słupkami (jeśli wymagane): 40 min; Czas na uszczelnienie obwodowe i krytycznych spoin (np. naroża): 60 min (mniej spoin do taśmowania niż przy SE); Całkowity czas (szacunkowo): 60 + 200 + 220 + 40 + 60 = 580 minut (ok. 9.7 godziny)
Z powyższego widać, że teoretyczna oszczędność czasu przy użyciu płyt T&G może być niewielka, ale idzie w parze z potencjalnie lepszą jakością połączeń pod kątem szczelności powietrznej.
Prawdziwe oszczędności przy T&G pojawiają się, gdy liczy się minimalizacja mostków powietrznych i przyspieszenie etapu prac wykończeniowych (mniej taśmowania).
Płyty SE natomiast są bardziej uniwersalne w zastosowaniach, gdzie dokładne dopasowanie i minimalizacja odpadów (np. na dachu z lukarnami i skosami) jest priorytetem, a szczelność zapewnia się innymi metodami (np. bardzo dokładne taśmowanie lub dodatkowe warstwy powietrzne).